Frequently Asked Questions
For Robotic Arm
1.Can the robotic arm be mounted inverted or horizontally?
Some models of robotic arms, such as the 2442, 6-axis series support inverted mounting but do not currently support horizontal mounting
2.Which programming languages are supported by the SDK development kit?
Currently, the SDK supports C#, C++, Java, LabVIEW, and Python. It is compatible with Windows, Linux, and Android systems.
3.Is the robotic arm controlled by a PLC?
Due to protocol restrictions, direct communication between a PLC and the robotic arm is not currently support. However, the arm can communicate indirectly with the standard software, HitbotStudio, or custom development software to control the robotic arm. The robotic arm itself is equipped with a certain number of I/O interfaces for signal interaction.
4.Can a single computer or industrial computer control multiple robotic arms?
HitbotStudio supports simultaneous independent control of multiple robotic arms. Simply create multiple working flows. Under one host IP, you can control up to 254 robotic arms (in the same network segment). The actual situation also depends on the performance of the computer.
5.Can the robotic arm be used in conjunction with machine vision?
Currently, the 4-axis robotic arm cannot directly cooperate with vision systems. However, users can communicate with the arm through HitbotStudio or custom-developed software to receive relevant vision data and control the robotic arm. Additionally, HitbotStudio software includes a Python programming module for developing custom modules directly.
6.What is the biggest advantage of the 4-axis robotic arm?
1.The height of 4-axis series can be customized.
The XX32 Z-axis can be customized to a height of 0.1-0.5m;The XX42, XX50, and XX60 Z-axis can be customized to a height of 0.1-1m. The XX42E Z-axis can be customized to a height of 0.11m, 0.21m, 0.31m, 0.41m, or 0.51m.
2.Deployable in an inverted position.
3.Lightweight, easy to use, occupying a small space
7.What is the biggest advantage of the 6-axis robotic arm?
Wide Range of Application:can be used in automative industry, food and beverage industry, medical and health care, and laboratory industry, research fields, etc.; meet various functional requirement assembly, picking and placing, screw twisting, and glue dispensing.
Larger payload, longer arm reach,higher precision
8.What's the hottest application of the hitbot 4-axis robot?
- Industrial production: such as parts handling, assembly.
- Medical Detection: such as tube capping,pipetting,sample inspection.
- Academic research: used for lab testing, college education.
- Retail application: coffee-making, food-handling,etc.
FAQ
For electric gripper
1.Is the electric gripper Z-EFG series waterproof?
No, it is not waterproof. For special requirements, please consult the sales personnel.
2.Where is the driver controller for the gripper located, and do I need to purchase it separately?
The driver controller is built-in and does not need to be purchased separately
3.Can the gripper ID and baud rate be modified?
Yeah, it can be adjusted by the control software.
4..If the electric gripper keeps working continuously, will the motor overheat?
Through professional testing, it has been determined that the Z-EFG series grippers, when continuously working in an ambient temperature of 30 degrees Celsius, have a temperature rise of no more than 35 degrees Celsius. T
5.Does the gripper product include the front-end gripping part?
No, it does not. Users need to design the gripping fixture according to the actual objects to be gripped. Inaddition, Hitbot also provides a small library of fixtures. Please contact the sales personnel for more information
6.Does the Z-EFG-100 gripper support I/O or pulse control?
Currently, Z-EFG-100 only supports control via 485 communication. Users can manually set parameters such as motion speed, position, and gripping force.
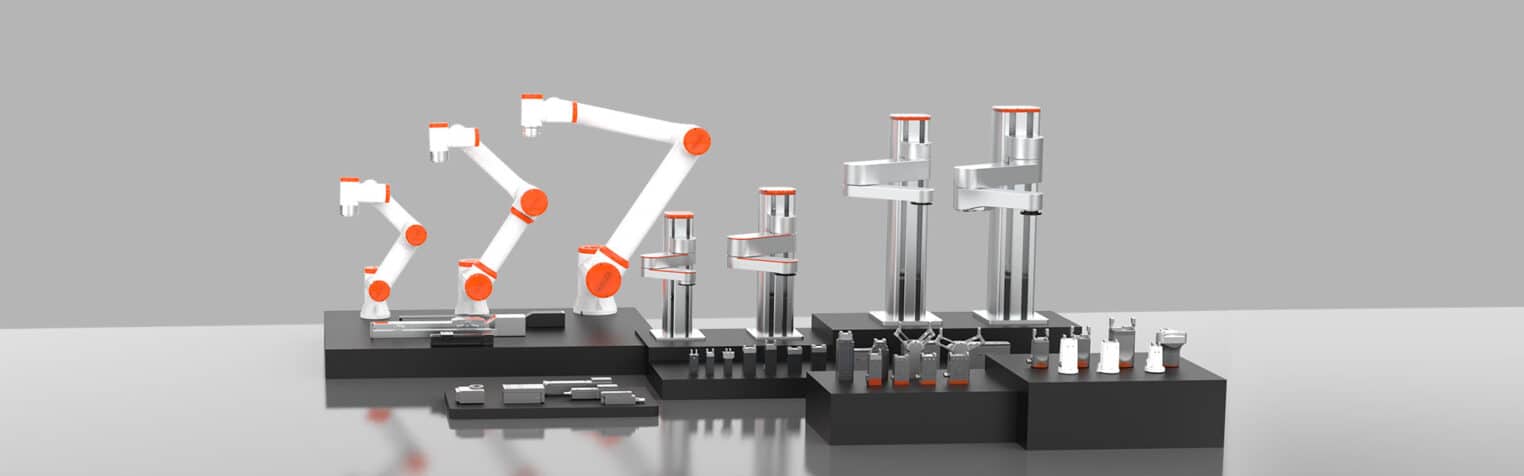