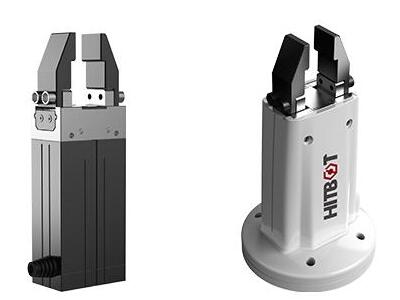
7 Key Advantages of Electric Grippers Over Pneumatic Grippers in Modern Automation
Why Smart Factories Are Switching to Electric End-Effectors
In the evolving landscape of industrial automation, grippers—the “hands” of robotic systems—have become critical for precision manufacturing. While pneumatic (air) grippers dominated factories for decades, electric grippers are rapidly gaining ground. By 2028, the electric gripper market is expected to grow at a 12.4% CAGR, outpacing pneumatic alternatives (MarketsandMarkets). This shift isn’t incidental; it’s driven by fundamental advantages in performance, sustainability, and adaptability. Let’s explore why electric grippers are becoming the go-to choice for Industry 4.0 applications.
7 Key Advantages of Electric Grippers Over Pneumatic Grippers in Modern Automation;
1. Precision Control & Force Modulation
- Electric Grippers:
– Closed-loop servo control enables real-time force adjustments (0.1N resolution).
– Programmable grip force profiles prevent damage to fragile items like glass panels or microchips.
– Repeatability of ±0.01mm ensures consistent handling in high-precision tasks (e.g., watch assembly).
- Pneumatic Limitations:
– Air pressure fluctuations cause ±15% force variance, risking part deformation.
– Requires additional regulators/valves for basic force tuning.
2. Energy Efficiency & Cost Savings
- Electric Grippers:
– 85% lower energy consumption: Only draw power during motion, unlike continuous air compression.
– Eliminate air leakage costs—a single leaking pneumatic line wastes $1,200/year in energy (DOE).
– No need for compressors, filters, or lubricators, reducing upfront infrastructure costs.
- Pneumatic Drawbacks:
– Compressors operate at 10-30% efficiency, with 70% energy lost as heat.
– Maintenance costs for air lines account for 22% of total ownership expenses (Festo).
3. Flexibility & Programmability
- Electric Advantages:
– One-tool adaptability: Adjust stroke, speed, and force via software for diverse product batches.
– Store 50+ preset profiles (e.g., soft grip for fruit vs. high-speed pick for metal parts).
– Collision detection: Auto-retract upon resistance, minimizing downtime from jams.
- Pneumatic Rigidity:
– Mechanical adjustments (springs, spacers) needed for task changes.
– Limited to binary open/close actions without costly add-ons.
4. Maintenance & Reliability
- Electric Systems:
– 10,000-hour MTBF (Mean Time Between Failures) due to fewer moving parts.
– Self-diagnostics alert users to wear (e.g., motor torque trends).
– Lubrication-free operation eliminates contamination risks in cleanrooms.
- Pneumatic Challenges:
– Seal replacements every 3-6 months in humid/dusty environments.
– Condensation in air lines causes corrosion and bacterial growth (critical in pharma/food).
5. Integration with Smart Factories
- Electric Grippers Enable:
– IoT connectivity: Monitor cycle counts, energy use, and predictive maintenance via OPC UA/MQTT.
– Digital twin synchronization: Simulate grip strategies before deployment.
– Data-driven optimization: AI analyzes grip patterns to reduce cycle times.
- Pneumatic Barriers:
– Limited data granularity (basic pressure switches only).
– Manual tuning can’t leverage machine learning.
6. Environmental & Ergonomic Benefits
– Silent operation (<50dB vs. pneumatic’s 75-90dB hissing).
– Zero oil mist emissions, complying with ISO 8573-1 Class 0 air purity standards.
– Lightweight designs reduce robotic arm payload strain.
7. Real-World Applications
Electronics: Samsung uses SCHUNK EGP grippers to handle OLED screens without micro-scratches.
Food Packaging: JLS Automation’s electric grippers pack biscuits at 200ppm with hygienic ISO 22000 compliance.
Pharma: Pfizer’s vaccine vial handling avoids particulate risks from pneumatic exhaust.
When to Choose Pneumatic Grippers
Despite electric dominance, pneumatics still excel in:
– High-force impacts: Forging presses (5,000N+).
– Explosive environments: ATEX-certified pneumatic systems.
– Ultra-low-cost setups: Simple pick-and-place under $500.
Conclusion
Electric grippers aren’t just an upgrade—they’re a strategic investment in future-proof automation. From unprecedented precision to energy savings and IoT readiness, they address the pain points of modern manufacturing. As product lifecycles shorten and customization demands grow, the agility of electric systems becomes indispensable.
Ready to transition? Explore our [Product Line] with patented anti-vibration algorithms and 24V DC compatibility. As the earliest electric gripper manufacturer in China, we provide various robotic grippers for various robot brands, including parallel grippers, rotation grippers, 3-finger grippers, Y-type grippers, wide grippers and collaborative grippers. Download the FREE ROI Calculator to compare 5-year costs vs. pneumatic systems.